Turkey’s trailblazing automotive manufacturer, Tofaş, was founded in 1968. 24.3% of Tofaş’s shares are traded on the İstanbul stock exchange and are included in both the BIST 30 and the BIST 100 indexes; control of the remaining shares is divided equally between Koç Holding and FCA Italy SPA. Tofaş’s publicly-traded shares are also included in the İstanbul stock exchange’s Corporate Governance and Sustainability indexes.
Tofaş’s production capacity, export performance, R&D competencies, and a workforce of nearly seven thousand people make it one of Turkey’s leading industrial concerns. Headquartered in İstanbul, Tofaş’s production operations are carried out in Bursa at a plant with 350 thousand m2 of enclosed space situated on nearly 1 million m2 of grounds.
As one of Stellantis’s foremost manufacturing and R&D centres, Tofaş creates added value for Turkey’s economy, industry, and R&D know-how by undertaking important roles in its parent’s global product-development projects.
Committed to being a leading player in all segments of its home market in line with customer expectations, Tofaş offers a broad portfolio of brands and products that include six brands (Fiat, Fiat Professional, Alfa Romeo, Jeep®, Maserati, Ferrari) for which it is the Turkish representative. Tofaş’s plant produces Fiat Doblòs and Fiorinos as well as the Fiat Egea family’s sedan, hatchback, station wagon and cross models. Egea is marketed in different regions of the world with the Fiat Tipo brand. Developed and manufactured at Tofaş, the Doblò is also exported to the United States, sold under the ProMaster City name.
The Tofaş R&D Center places second in the “R&D: Big R&D Centers” category in the 2020 round of the R&D and Design Centers Performance Index Awards handed out every year by the Ministry of Industry and Technology. Tofaş is the only automotive company to make it into the ranking.
Kemal EkbiÇ graduated BS in Business Administration from the State University of New York at Buffalo. Specialised in Financial analysis and Management Information Systems. In addition, he is a specialist in strategic planning, the realisation of R&D projects and project management. He has been with Tofaş since 1999 and has been responsible for the Tofaş R&D centre since 2005. He is an H2020 Trainer in Tofaş Academy
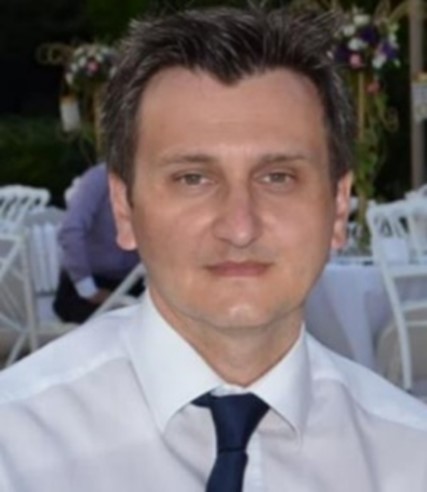
Hello, Kemal. Thank you so much for your time. I would like to start with your motivation to participate in the REVOLUTION project. Which aspects were key for your participation within the REVOLUTION concept.
“Good morning, Andrea. Nice to be here with you answering your questions. For me, applying all the knowledge collected during the last 22 years (including national and EU H2020 projects) and assisting in the successful implementation of REVOLUTION will open a new chapter in my professional career, letting me know different ways to work and establish strong connections with other manufacturers across the Automotive Industry.“
In the framework of your enterprise’s main activities, which could be the improvement from REVOLUTION?
“Recent EC initiatives confirm a further commitment to meet ambitious CO2 reductions in transport by setting targets to reach at least a 60% reduction in GHG emissions in transport by 2050 relative to 1990. This regulatory push has been a catalyst for OEMs to invest heavily into strategies for emission reductions, through the light-weighting of Internal Combustion Engine (ICE) vehicles and through the adoption of alternative/electric powertrains. As a result, the number of Electric Vehicles (EVs) across Europe is on the rise however, only ~2% of the EU vehicle fleet currently covers EVs. Tofaş has been planning to develop automotive components, using polymer solutions that feature optimised recycled materials to increase light-weighting opportunities that extend the range and efficiency of Electric Vehicles and improve end-of-life separation of components to facilitate proper dismantling and the material’s reuse, recovery, and recycling.”
“…Tofaş has been planning to develop automotive components, using polymer solutions that feature optimised recycled materials to increase light-weighting opportunities that extend the range and efficiency of Electric Vehicles and improve end-of-life separation of components to facilitate proper dismantling and the material’s reuse, recovery, and recycling.”
Kemal EkbiÇ
Being a car manufacturer, which are the attractive points of REVOLUTION solutions?
“REVOLUTION will demonstrate new methods and approaches to greater inclusion of recycled materials and component light-weighting. Based on the materials (rPP/rPA) demonstrated in REVOLUTION, it is expected that these materials could be rolled-out to lower bumper and crash boxes across the entire TOFAŞ future product range. REVOLUTION outputs will allow Tofaş to achieve cost-effective production of the crash box and lower rear bumper. The switch from virgin to recycled materials will allow for a cost saving of between 10-20% per part manufactured. Additionally, the 66% reduction in crash-box production cycle-time will streamline production, reduce costs and improve vehicle lead times. Collectively, these elements enable TOFAŞ to achieve a considerable step change in global competitiveness. The development of a new thermoplastic-based crash box is novel across FCA, creating substantial future opportunities for Tofaş and FCA. With the future merger of FCA and PSA, several new applications for REVOLUTION developments will be opened, especially across EV models.lxiv PSA Group has announced that all brands (Peugeot, Citroën, DS Automobiles, Opel and Vauxhall) will have electrified options based on a shift to a new EV architecture and vehicle platform.”